Gast Air Motors
We provide the highest quality pneumatic gast air motors available on the market today. Our motors are designed to provide maximum efficiency and performance, while also offering superior durability and reliability.
Our pneumatic gast air motors are ideal for a wide range of applications, including industrial, commercial, automotive, and aerospace. Gast Air Motors provide powerful and reliable performance for a wide variety of applications. These motors are ideal for applications requiring a high torque output with low air consumption. Gast Air Motors are designed to be rugged and reliable, and their pneumatic design ensures they are easy to maintain and service. Gast Air Motors offer an energy efficient solution for applications requiring a high torque output. Gast Air Motors are lightweight, low-maintenance, and can be used in many different environments. Gast Air Motors offer a wide range of advantages, such as reliable operation, long life, and minimal noise.
Gast Air Motors are available in a range of configurations, including single and double acting designs. Single acting motors operate on compressed air in one direction and can produce up to 18 horsepower. Double acting motors use the same compressed air source for both directions and can generate up to 30 horsepower. Gast Air Motors are also available in a variety of speeds and torque ratings, allowing for a tailored solution to any application.
1. AIR MOTOR TECHNOLOGY
Gast rotary vane air motors use compressed air to produce rotational motion of a shaft, by utilizing axial vanes fitted into a slotted rotor, which mounts eccentric with the bore of the motor’s housing, and the vanes extending to seal against the housing bore with springs, cam action, or air pressure to develop torque from the pressure of the compressed air acting on one side of the vanes causing the rotor to spin.
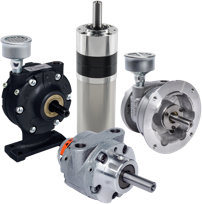

2. COMPRESSORS & VACUUM PUMPS
Compressors and vacuum pumps are essential pieces of equipment for a wide range of industries. They provide the pressure and vacuum necessary for a variety of
industrial processes, from air conditioning and cooling to chemical manufacturing and food production. Compressors are used to increase the pressure of a gas or vapor, while vacuum pumps are used to reduce the pressure. Compressors and vacuum pumps are easy to maintain and provide a cost-effective solution to many industrial needs. They are also reliable and durable, making them an ideal choice for any industrial setting.
3. BLOWER TECHNOLOGY
In a regenerative blower, the impeller blades and the walls of the housing form a hollow, circular ring that serves as the compression space. The impeller draws in
air from the inlet port and accelerates it outward using centrifugal force. This process is known as regenerative, as some air slips past each impeller blade as it
rotates and is reaccelerated by the succeeding blade. This air is then expelled from the blower at a higher velocity than it was taken in.
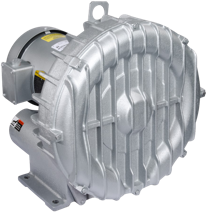
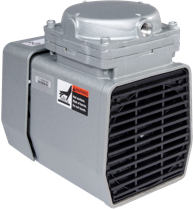
4. DIAPHRAGM TECHNOLOGY
Diaphragm compressors are a variation of standard piston compressors with the primary difference being the addition of a flexible diaphragm membrane in the head of the pump in lieu of a traditional piston. A connecting rod and eccentric shaft convert the rotational motion of an electric motor into reciprocating motion, which moves the diaphragm up and down. When used as a compressor, as the diaphragm moves down a vacuum is created above it allowing outside air at atmospheric pressure to push open the inlet valve and fill the area above the diaphragm. As the connecting rod and diaphragm move up, the air in the pump head compresses forcing the inlet valve shut and pushes the discharge valve open. The compressed air then moves from the discharge port into the air line or the receiver tank depending on the system design. With each stroke, more air enters the air line or receiver tank and the air pressure rises.
5. PISTON COMPRESSOR TECHNOLOGY
Piston compressors are positive displacement compressors that utilize the same operating principle as an internal combustion engine. Similar to an internal combustion engine, the compressor has a crankshaft, connecting rod and piston, a cylinder and a valve head. The crankshaft, driven by either an electric motor or a pulley, transfers rotational motion into reciprocating motion driving the piston up and down in the cylinder. As the piston moves down, a vacuum is created above it allowing outside air at atmospheric pressure to push open the inlet valve and fill the area above the piston. Specially designed piston rings seal the gap between the piston and the cylinder wall and as the piston moves up, the air above it compresses forcing the inlet valve shut and pushes the discharge valve open. The compressed air then moves from the discharge port into the air line or the receiver tank depending on the system design. With each stroke, more air enters the air line or receiver tank and the air pressure rises.
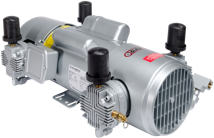
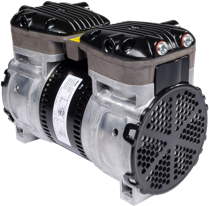
6. ROCKING PISTON COMPRESSOR TECHNOLOGY
Rocking piston compressors are a variation of standard piston compressors. Instead of having a separate piston and rod that are connected via a wrist pin, rocking piston compressors utilize a solid cast piston rod that incorporates both the piston and rod. A flexible cup seal attached to the piston rod provides a seal between the piston rod and cylinder and also guides the piston rod as it is driven up and down in the cylinder. The piston rod is mounted to an eccentric bearing assembly,
which converts rotary motion from either an AC or DC motor into the linear motion that drives the piston within the cylinder. As the piston moves down, a vacuum is created above it allowing outside air at atmospheric pressure to push open the inlet valve and fill the area above the piston. As the piston moves up, the air above it compresses forcing the inlet valve shut and pushes the discharge valve open. The compressed air then moves from the discharge port into the air line or the receiver tank depending on the system design. With each stroke, more air enters the air line or receiver tank and the air pressure rises.
7. ROTARY VANE TECHNOLOGY
Pumping action is produced by a series of sliding, flat vanes as they rotate in a cylindrical housing. An eccentrically mounted rotor turns and the individual vanes slide in and out of their slots by centrifugal and pressure-loading forces. This creates a series of air compartments of unequal volume against the wall of the housing. These compartments get larger during the suction part of the cycle, creating vacuum at the intake port. The compartments get smaller during the discharge portion of the cycle, creating pressure at the exhaust port. The vacuum and pressure flows are free of pulsation because the inlet and exhaust ports do not have valves, and the air is moved continuously rather than intermittently
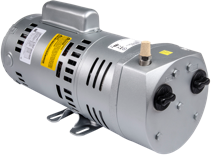
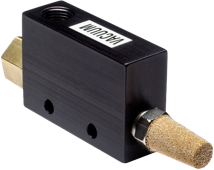
8. ACUUM GENERATOR TECHNOLOGY
Gast vacuum generators have a patented design that incorporates a series of venturi nozzles and no moving parts. When compressed air is forced through these nozzles, its velocity increases and a decrease in pressure occurs. Each nozzle has a progressively larger orifice selected to extract the maximum amount of energy from the compressed air while optimizing the levels of vacuum generated. This patented design allows Gast vacuum generators to generate powerful vacuum levels with a high degree of efficiency and minimal maintenance.
9. TANK SYSTEMS
Tank systems provide a great way to get the most out of your small pumps. Gast and Jun-Air offer a variety of tank systems that are designed to maximize the
efficiency and power of your pumps. Whether you’re using Piston or Rocking Piston technology, these systems come in a range of tank sizes to suit your requirements. Additionally, Gast’s dry sprinkler tank systems are specially designed for dry sprinklers. Jun-Air’s clean and quiet compressors are ideal for medical, dental, and laboratory applications and come with a two-year warranty. With tank systems, you can easily get the most performance out of your pumps.
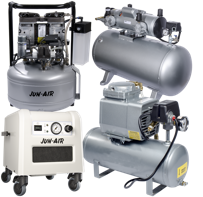
Gast Air Motors are powered by compressed air, meaning that they are extremely efficient and produce very low levels of noise. This makes them ideal for applications where noise is an issue, such as in medical and laboratory environments. They also require very minimal maintenance and can operate over a wide range of temperatures, making them suitable for a variety of applications.
Gast Air Motors are designed to be safe and reliable, making them an ideal choice for applications requiring power and performance. Their simple and compact design ensures they are easy to install, and their pneumatic design ensures they are economical to operate. Gast Air Motors are also designed to be reliable in harsh environments, making them a great choice for industrial and commercial applications.
Our pneumatic gast air motors are designed to be lightweight, yet powerful. They are constructed of high-quality materials, such as aluminum and stainless steel, to ensure maximum strength and durability. Our motors also feature an adjustable speed control, allowing you to tailor the performance to your specific needs.
We are proud to offer the best pneumatic gast air motors available. We strive to provide our customers with the highest quality products and services. If you have any questions or need assistance selecting the right motor for your application, please don’t hesitate to contact us. We are here to help!